|
После второго
рабочего дня в Болгарии, нас, как водится, повезли на неофициальную
часть в ресторан. Национальные блюда, вино, танцы и музыка
пронеслись яркой чередой, и вот мы сидим в автобусе, пытаясь
проехать по узким улочкам обратно в отель. Автобус, не вписываясь
на повороте, застрял. Его дальнейшему продвижению мешала машина,
неудачно припаркованная на обочине. Для того чтобы проехать,
не хватало каких-то 20 см, и пассажиры, члены клуба CIO металлургии,
взялись помочь водителю и решить проблему. Одни принялись
рассчитывать правильную траекторию, другие взялись за машину,
пытаясь закинуть ее на бордюр, остальные давали советы, сидя
в автобусе. В итоге орущая сигнализацией машина осталась на
месте и автобус, сделав несколько итераций, выехал, не поцарапав
легковушку. И если бы мы были более рассудительными и, прежде
чем кидаться сдвинуть машину, внимательно оценили все расстояния
и зазоры, то выехали бы, не испачкав рук и не пугая прохожих.
Это лирическое отступление иллюстрирует тему
третьего заседания CIO металлургии, посвященного MES-системам.
Наши металлургические предприятия похожи на этот неповоротливый
автобус, и для того чтобы он двигался и продолжал развиваться,
нужно внедрять решения и преодолевать препятствия. И устранение
этих преград очень часто происходит наскоком, засучив рукава
и не особо задумываясь об оптимальности принятого решения.
И если в случае с автобусом нам полезно было перед сном размяться,
то с предприятиями все сложнее — зачастую потери от этих неправильных
решений составляют миллионы долларов.
Итак, 17—18 сентября недалеко от г. Варна (Болгария) прошло
третье заседание клуба CIO металлургии, посвященное MES-системам.
Мероприятие было организовано фирмой Оптима-интеграция при
поддержке компаний SAP, HP, Intel, Cisco Systems, OXS, APC,
PSI и Промэлектроника.
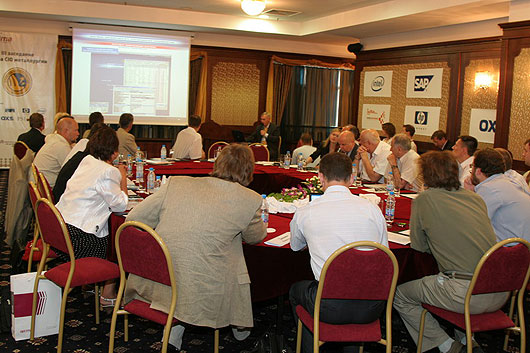
В рамках заседания, помимо вендоров и поставщиков решений
для промышленной автоматизации, выступили с докладами И. Суковатин,
CIO НТМК (с докладом, посвященным системе производственного
планирования), Ю. Сарапулов, CIO Выксунского ТЗ (темой выступления
стал первый этап внедрения MES-системы от компании Broners
Metals) и др. На круглом столе, модератором которого был главный
редактор журнала Intelligent Enterprise К. Зимин, обсуждались
вопросы, касающиеся подхода к определению основных задач MES-систем
на металлургических предприятиях, особенности календарного
и производственного планирования, учет попередельного производства,
взаимодействие с поставщиками решений и др.
В мероприятии приняли участие около 30 специалистов, представляющих
интересы компаний НТМК, ОМК, ТМК, Норильский никель, Русал,
Уральская Сталь, Группа ЧТПЗ, Северский и Синарский трубные
заводы, Таганрогский МЗ, ОМЗ-Спецсталь и др.
Здесь мы публикуем часть мнений, высказанных в рамках круглого
стола.
И.
Суковатин, CIO ОАО «НТМК»
Из нашего опыта создания и использования MES-систем приведу
два примера — удачный и неудачный. Начну с неудачного. Примерно
20 лет назад перед нами была поставлена задача оптимизировать
раскрой на блюминге «1500» заготовки таким образом, чтобы
при последующей прокатке на универсально-балочном стане и
порезке получить максимальный выход заданных мерных длин.
Задача математически сложная (целочисленное нелинейное программирование)
и интересная, эффект от ее решения казался очевидным. Потратили
много времени, но в итоге создали систему, которая измеряет,
кроит, режет — все замечательно.
Но после нескольких дней работы обнаружилась проблема. В результате
решения математической задачи, заготовки одного и того же
назначения после порезки каждого раската получались немного
разной длины. Возникли проблемы учета и отслеживания разнодлинных
заготовок на универсально-балочном стане. Также выяснилось,
что погрешности измерений, технологические отклонения в режимах
нагрева и прокатки заготовок на стане сводят «на нет» выгоду
от точных математических расчетов. Оказалось проще ввести
в систему таблицу нормативных длин заготовок и вести порезку
раскатов на блюминге, исходя из ее данных.
Второй пример — удачный. Это система динамического планирования
в сталеплавильном производстве. Задача заключается в планировании
работы агрегатов конвертерного цеха (четырех конвертеров,
трех агрегатов «печь-ковш», двух вакууматоров и четырех МНЛЗ)
так, чтобы обеспечить непрерывную разливку стали одновременно
на всех МНЛЗ.
При реконструкции конвертерного цеха НТМК (строительстве МНЛЗ
и агрегатов внепечной обработки) проблеме синхронизации работы
агрегатов, обеспечивающих непрерывную разливку, не было придано
серьезного значения. Но после пуска первой же МНЛЗ выяснилось,
что при традиционной организации работы удавалось непрерывно
разлить серию не более чем из десяти плавок, а нужно было
100—120 плавок. Тогда и потребовалось срочно создать систему,
синхронизирующую работу всех агрегатов в режиме реального
времени, исходя из текущего состояния производства. Эта задача
была решена. Теперь, в отдельные сутки, в конвертерном цехе
НТМК непрерывно разливается до 88 плавок стали одновременно
на четырех МНЛЗ, что позволит после реконструкции конвертеров
выплавлять и разливать до 4,2 млн т стали в год.
Эти примеры иллюстрируют нашу главную задачу при создании
MES — правильно выбирать направление своих усилий, верно определять
задачи и предвидеть проблемы и результаты.
Последний наш MES-проект — это система динамического планирования
производства. Основные идеи — производство, ориентированное
на клиентов, оптимальное планирование от текущего состояния
производства и сбыта, оперативно календарное планирование
по критерию максимальной скорости движения оборотных средств.
Система большая и сложная, но с точки зрения пользователей
достаточно простая и удобная. Сейчас она в работе.
Среди проблем, которые хотелось бы выделить в ходе освоения
и промышленной эксплуатации — организационные, психологические
и политические. Дело в том, что в работе с системой планирования
участвуют несколько групп заинтересованных лиц (производственники,
коммерсанты, экономисты), а их интересы к результатам планирования
существенно различаются.
В такой же степени различаются их представления о лучшем варианте
производственной программы и лучшем графике производства.
А если портфель заказов сформирован и производственные ограничения
заданы, то процедуры моделирования производственных программ
и графиков легко доступны любому пользователю любой группы
заинтересованных лиц. Отсюда возникает проблема разделения
прерогатив на принятие решений без снижения эффективности
планирования.
Далее: клиентоориентированное планирование предполагает построение
производственных графиков не только в виде физических объемов
производства по суткам, но, в первую очередь, в виде графиков
исполнения заказов. Такое планирование требует более жесткой
дисциплины исполнения графика, смещение усилий в направлении
подготовки производства для его реализации.
Кроме этого, оптимальный график производства предполагает
минимизацию запасов полуфабрикатов в процессе производства.
Соответствующие службы, напротив, по понятным причинам стремятся
держать запасы на возможно более высоком уровне.
Есть еще много аналогичных проблем, не технических, но которые
обязательно требуют решения, чтобы управление производством
было максимально эффективным.
Ю.
Сарапулов, CIO ОАО «ВМЗ»
Выксунский МЗ приступил к реализации проекта «Интегрированная
Автоматизированная Система Оперативного Управления Производством
ТЭСК ТБД» (MES), назначение которого — объединить управления
разных уровней в единую информационную систему, решающую задачи
оперативного планирования, управления производством цеха,
сбора, обработки, хранения технологической и производственной
информации, предоставления оперативной и актуальной информации
диспетчерам, руководителям, менеджерам ТЭСЦ-4 и топ-менеджерам
завода. Кроме того, с его помощью будет вестись оперативное
планирование работы ТЭСК ТБД. Основные функции системы — автоматизация
технологического процесса, информационное прослеживание штрипса
и трубы, мониторинг, диспетчеризация и анализ производства,
а также оперативное планирование производства. Общий срок
выполнения работ — около 17 месяцев. Мы рассчитываем, что
экономический эффект будет получен за счет снижения времени
определения причин остановок или задержек производства, оперативного
принятия решений по их устранению, анализа истории аварийных
ситуаций и выявление «слабых» мест; перехода от эпизодической
к систематической диагностике оборудования в реальном времени
(контроль наработки оборудования на отказ, его сравнение с
паспортными данными); повышения ремонтопригодности систем
автоматики (замена разнородных контроллеров на типовые); снижения
простоев на 10% перевалках за счет более четкого формирования
планов работ системой оперативного планирования и расстановки
очереди производственных заказов.
Основные проблемы при внедрении типового MES-решения следующие.
Во-первых, надо найти действительно разбирающегося в вопросе
партнера, с багажом уже проверенных решений и специалистов
высокого класса. Во-вторых, необходимо грамотно и наиболее
выгодно для предприятия заключить с ним контракт — тоже непростая
задача, ведь зачастую определить границу — что является обязанностью
партнера, а что должен выполнить сам заказчик — довольно сложно.
Но сделать это нужно, во избежание недопонимания, несогласованности,
которые существенно тормозят проект.
Г.
Глезер, начальник управления информационных технологий ЗАО
«ТМК»
Если в целом говорить о MES-системах, то это, в первую очередь,
возможность владения менеджерами высокого уровня достоверной
информации о производстве. Но в каждом конкретном случае следует
определить, стоит ли овчинка выделки. В ТМК мы старались подойти
осмысленно к проектированию, внедрению и эксплуатации MES.
И решили создать документ «Концепция построения АСУТП и MES-систем».
При рассмотрении всех связанных с этим вопросов, обнаружили,
что прежде всего надо определиться, что такое MES-системы.
Каждый автор публикации на эту тему по-разному трактует это
понятие, и нам в рамках ТМК важно было сформулировать, что
мы понимаем под понятием «MES». Следующая задача — определить
цели и задачи построения этих систем в ТМК. И только потом
имеет смысл начинать предпроектное обследование, в котором
также есть свои нюансы. Мы решили посмотреть, как классифицировать
выделенный объект управления, по каким составляющим и направлениям
и, исходя из этих показателей, выявить слабое звено. Следующий
вопрос — определить, что мы имеем с точки зрения существующей
системы управления этим объектом. Опять-таки идет определенная
классификация, по которой эту систему надо рассматривать.
И вот сопоставляя то, что мы имеем по объекту управления,
с тем, что есть у нас по системе его управления, можно понять,
целесообразно ли заниматься внедрением MES в данном конкретном
случае. В итоге получаем список, из которого выбираем, что
же является узловой проблемой, главной задачей, с которой
надо начинать. Мы начали с этого документа, и на его базе
разработали методику обследования предприятия. Данный подход
позволяет идти к построению MES не от конкретных производственных
задач, а более комплексно, от глобальных задач всего предприятия.
Б.
Славин, CIO Группа ЧТПЗ
На трубном производстве требования к разработке MES-систем
существенно зависят от технологии изготовления конкретной
продукции. Например, при выпуске ТБД одной из основных проблем,
решаемой на MES-уровне, является прослеживаемость, идентификация
и контроль характеристик. Стоимость ТБД немалая, а требования
к изготовлению и оформлению техпаспортов достаточно высокие.
Отсутствие оперативности или ошибки в составлении документации
приводят к необоснованным потерям. Если же говорить, например,
о волочильных цехах, то там на MES-уровне первостепенными
становятся задачи оптимизации расчета длины и обрезки труб,
эффективность выбора технологических маршрутов. Функции MES-систем,
в отличие от ERP-уровня, в рамках одной компании отличаются
от цеха к цеху и требуют эксклюзивного подхода.
Единственное возможное преимущество MES перед ERP-системами
— это то, что для них легче посчитать отдачу от внедрения.
Не всегда, конечно, но в большинстве случаев это так. Например,
проблемы с идентификацией и прослеживаемостью ТБД приводят
к существенным задержкам отгрузки и увеличению складских запасов
— потери легко представить в денежном эквиваленте. Отсутствие
оперативной информации о параметрах изготовления горячекатаных
труб приводит к превышению количества брака, снижению сортности
и, как следствие, к стоимостным издержкам. Поскольку для MES-систем
почти всегда можно составить технико-экономическое обоснование,
понять, какой эффект мы получим от использования цеховой информационной
системы, принятие решения о внедрении MES-систем, как правило,
более объективно.
Л.
Перепелицына, ЗАО «ОМК»
Архитектура MES-систем имеет весьма широкую функциональность.
В случае, когда информационная система управления предприятием
строится от производства, можно определить функции, которые
будет выполнять MES-система, а остальные закрыть другими ИС.
Исторически, на мой взгляд, большинство метпредприятий на
первом этапе создавали или внедряли учетные системы, частично
закрывающие и функционал MES-систем. Следовательно, часть
функций, которые принято приписывать MES-системам, уже решена
ERP-системами или программным обеспечением индивидуальной
разработки.
Основная задача MES — это, как мне кажется, управление производственным
процессом, диспетчеризация и планирование — то, что сейчас
очень востребовано на предприятиях. И эти задачи не должны
носить локальный характер (автоматизировать управление отдельными
технологическими процессами). Наоборот, они интересны с точки
зрения управления всеми производственными процессами предприятия.
И поскольку эти процессы достаточно хорошо документированы,
необходимо продолжить их формализацию и автоматизировать.
Конечно, задачи автоматизации можно решать поэтапно, начиная
с основных производственных процессов, но ведь производство,
тем более попередельное, нельзя дробить и автоматизировать
частями, нужен комплексный подход к автоматизации всей технологической
цепочки. Следовательно, в настоящее время для предприятий
это самые необходимые функции MES-систем.
Еще хотелось бы отметить изменение требований топ-менеджмента
предприятий к производственной информации. До недавнего времени
в цехах имелись свои локальные учетные системы, системы уровня
АСУТП и этого было достаточно для управления. Но сегодня интенсификация
производства резко повысила требования к управлению производственными
процессами не только в отдельных цехах, но и на всем предприятии.
Выстраиваются прозрачные системы управления на всех уровнях,
интегрируя в себя производственные системы, АСУТП. Основные
резервы роста эффективности находятся в совершенствовании
управления производственными процессами, остальные уже исчерпаны.
Данные задачи осмыслены, выделяются средства для их решения,
меткомпании начинают вести проекты создания производственных
систем, в том числе используя уже разработанные MES-системы.
Н.
Сарапулова, главный специалист по проектированию корпоративных
информационных систем ЗАО «ОМК»
Предназначение MES-системы на предприятии, уже имеющем развитую
ERP-систему (выполняющую основные учетные функции), заключается
в решении задач, связанных с оперативным планированием работы
цехов и агрегатов, прослеживании движения, текущего состояния
и местонахождения продукции на всех этапах ее производства.
А также в решении задач, связанных со сбором и накоплением
данных о характеристиках, параметрах технологических процессов,
состоянии оборудования и качестве товара. К примеру, при производстве
трубы ответственного назначения, мы обязаны 50 лет хранить
паспорт ее изготовления, который создается на основе информации,
снятой в автоматическом режиме с датчиков, полученной из контроллеров,
лабораторных проб и испытаний, акцептов ОТК и т.п. Из ERP-системы
необходимо исключить все, что можно вынести в MES, чтобы не
перегружать ее не свойственными ей расчетами и массивами данных.
И при использовании в качестве хранилища этих данных ERP-систему,
автоматически снижается ее производительность. С легкой руки
консультантов, ERP-системы очень часто претендуют на решение
части задач, которые несвойственны и не нужны им. Интерес
консультантов тут очевиден, однако хочется предостеречь коллег
и порекомендовать применять для решения конкретных задач соответствующие
инструменты. Задачи управления производством — не для ERP-систем,
потому как они требуют неоправданно больших мощностей и не
могут быть решены в тех деталях, которые требуются производственникам.
Заключение
В рамках круглого стола были, конечно же, затронуты не только
вопросы, касающиеся применения MES на метпредприятиях, но
и вопросы управления качеством, планирования и управления
производством, диспетчеризацией, взаимоотношениями с подрядчиками
и т.д. Еще больше тем поднималось в неформальном общении,
недостатка которого, благодаря организаторам заседания, не
было.
Е.
Селиванов, директор департамента промышленности Оптима-интеграция,
председатель клуба CIO металлургии
Мы выбрали тему MES на прошлом заседании в Венгрии, и видим,
что не ошиблись — эта тема одна из самых актуальных для членов
нашего клуба. Несмотря на то, что ее уже описали сотни трудов
и исследований, личный опыт коллег всегда намного интереснее
и важнее того, что говорят другие. ERP, например, можно внедрять,
ориентируясь на опыт нефтяников и машиностроителей. А вот
MES — это системы, напрямую связанные с особенностями металлургического
производства и тут уже гораздо более важен отраслевой акцент.
Следующее наше заседание пройдет под флагом ITSM. Эта тема,
помимо своего прямого назначения, актуальна еще и в связи
с тем, что аудит качества управления ИТ-службой на предприятии
входит в общий аудит, предшествующий получению предприятием
стандарта менеджмента качества ISO 20000. А вопрос повышения
качества, и, следовательно, получение подтверждающих это качество
международных сертификатов, является одним из приоритетных
для металлургов в связи с грядущей интеграцией в ВТО, с быстро
растущими объемами китайской металлопродукции и с повышающейся
внутренней конкуренцией.
Фоторепортаж с III-го заседания клуба CIO
металлургии
17—18 сентября, г. Варна (Болгария)
Дополнительные
материалы:
|
|