|
Лев Бондаренко, Бизнес-директор, БДО Юникон
Профессия кладоискателя стремительно теряет свою актуальность. В любом цеху металлургического завода можно найти гораздо больше, главное знать, где искать.
Изношенное оборудование, большая доля устаревших производств (доменное производство), низкий уровень качества продукции высоких переделов, отсутствие эффективных мотивационных механизмов, повышение цен и тарифов на энергетические, топливные и транспортные ресурсы представляют собой лакомый кусочек для специалистов по сокращению производственных затрат и снижению себестоимости продукции.
Конечно, повышать эффективность можно разными путями. Можно и совершенно необходимо вкладывать средства в модернизацию оборудования, ввод в производство новых, перспективных технологий (например, агрегатов комплексной обработки стали или машин непрерывного литья заготовки, совмещенных с прокатными станами), но это долгосрочные инвестиции, и эффект от них проявится через много лет, а предприятиям необходимо сокращать издержки уже сейчас. Достаточно быстро получить экономический эффект, не прибегая к дорогостоящим инвестициям, можно, используя современные технологии управления затратами.
Внимание к мелочам, хорошее знание технологии производства, элементы социального инжиниринга — вот основные инструменты современного затратоискателя.
Возьмем ручку и карандаш и отправимся в увлекательное путешествие по традиционным местам возникновения затрат металлургического завода.
Баланс четырех стихий
Раньше люди верили, что весь мир построен из четырех основных стихий: воды, земли, воздуха и огня. Все, что происходит в природе, объясняли их взаимодействием.
Четыре стихии металлургии — это производство, торговля, качество и себестоимость. Производственная составляющая тяготеет к загрузке производства с минимальным количеством переналадок оборудования, в прокатном производстве — перевалок станов, в сталеплавильном — максимальной загрузке печей и сокращению выплавляемых сплавов. Торговая составляющая традиционна: выполнение заказа точно в срок, максимальное удовлетворение потребностей клиента по выпускаемому сортаменту и максимальный маржинальный доход. Себестоимость подразумевает минимизацию затрат на производство одной единицы продукции. Качество — наиболее точное соответствие продукции стандартам и техническим условиям изготовления.
Эффективность работы завода определяется тем, насколько сбалансированы продажи, загрузка производства, себестоимость и качество. В идеале точка принятия решения должна учитывать, насколько привлекательно для клиента предложение, насколько эффективно можно загрузить производство, не будет ли работа осуществляться себе в убыток, и сможет ли производитель выполнить заказ с соблюдением необходимых норм качества.
Усиление влияния одной из составляющих неизбежно приводит к ослаблению в перспективе остальных показателей. Отдайте приоритет эффективной загрузке производственных мощностей и неизбежно получите длительные сроки изготовления заказов и сокращение выпускаемого сортамента, а в будущем — критическое сокращение портфеля заказов и недозагрузку производства. Переориентируйте завод на максимальное удовлетворение клиента и неизбежно получите проблемы в загрузке производства и, как следствие, — снижение прибыльности предприятия и заметное ухудшение качества продукции.
Для того чтобы выбрать наиболее эффективное направление поиска затрат на заводе, необходимо определить, за счет какой службы возник дисбаланс. В идеале генеральный директор завода как раз и должен следить за тем, чтобы баланс интересов всегда сохранялся. Но на практике существует видимый перекос в производственную или коммерческую составляющую. Часто это объясняется опытом генерального директора и его первых заместителей.
Определив причину дисбаланса, достаем лопату и начинаем копать в этом направлении.
Простой вопрос
Вы никогда не задумывались над тем, почему самые сложные теории начинаются с очень простых вопросов? Придите на любой завод и спросите у технолога, каков средний цикл производства изделия на их заводе. Теперь идите в коммерческую службу и задайте тот же самый вопрос.
Как правило, цикл производства «лом — сталь — прокат» составляет не более семи дней. В договоре же с клиентом указывается, что производство заказа составляет не менее одного месяца. Для разных сортаментных групп этот гарантированный срок может составлять до четырех месяцев. Немного вникнув в детали, можно выяснить, что срок изготовления заказа вычисляется на основании плановых нормативов. То есть заранее просчитанных максимальных сроков изготовления продукции для каждой сортаментной группы. Причем этот максимальный срок складывается из максимальных сроков производства на каждом переделе с учетом всех возможных причин задержки, которыми так изобилует металлургическое производство.
Разница существенна, не правда ли? Если, например, при покупке автомобиля вам указали бы не конкретную дату, когда вы можете забрать долгожданное авто, а приблизительный квартал, вы бы страшно возмутились и, наверное, выбрали бы другого производителя. А в металлургии ничего, как-то все притерпелись.
Плановые нормативы сроков производства являются наиболее заметным показателем эффективности завода и напрямую влияют на затратную составляющую производственного процесса. Попробуем разобраться в этом на примере работы прокатного цеха.
Сбалансированное производство
Целый пласт производственных затрат связан с несбалансированными мощностями производственных участков. Для того чтобы понять механизм их возникновения, разберем следующий пример. Предположим, в цехе работают два стана. Первый стан выпускает полуфабрикат для второго. Предположим также, что первый стан производительнее второго на 20%. Если оба стана работают с максимальной производительностью, то со временем между первым и вторым образуется буферная зона хранения металла, который второй стан не будет успевать обрабатывать. Этот необработанный металл фактически является связанным капиталом, поскольку предприятие не в состоянии его переработать в готовую продукцию и при этом не может вложить деньги в закупку того, что действительно необходимо на данный момент.
Фактически деньги, вложенные в этот металл, перестают приносить прибыль и увеличивают затраты.
Для того чтобы избежать возникновения затрат, необходимо сбалансировать производительность обоих станов. Например, можно использовать балансировку на уровне мотивационных механизмов. Обычно в цехе зарплата рабочих привязывается к операционным нормативам. Другими словами, чем больше обработает металла бригада на быстром стане, тем больше денег она получит по итогам месяца. Однако в приведенном примере производство излишка металла приносит заводу убытки, и мотивировать бригаду на его выпуск фактически не имеет никакого смысла. Следовательно, мотивационный механизм для бригады более быстрого стана должен поощрять обработку металла в объемах, которые может успеть переработать второй (менее производительный) стан, и демотивировать необоснованное перепроизводство.
Разобравшись с причинами возникновения затрат из-за несбалансированного производства, можно составить карту возникновения затрат цеха.
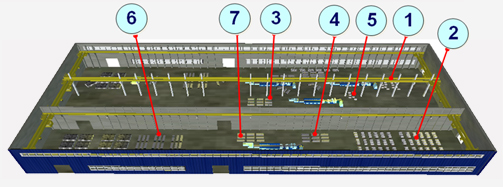
Для чистоты эксперимента предположим, что изучаемый цех недавно построен и только начал выпускать готовую продукцию. Объем незавершенного производства будет минимален, и заказы станут закрываться точно в срок.
По мере работы цеха начинают увеличиваться запасы металла после станов с наиболее высокой пропускной способностью (1). Количество сданной готовой продукции при этом увеличиваться не будет, поскольку оно определяется скоростью работы самого медленного участка цеха. Однако более быстрые участки уже переработали весь металл и простаивают из-за отсутствия необходимого сырья.
Руководство завода видит, что склады сырья пусты, и принимает решение о закупке достаточного количества сырья для бесперебойной работы цеха (2). При этом ожидается, что увеличится и выпуск готовой продукции. Однако вместо этого растет объем незавершенного производства.
Естественно, такая ситуация руководство не устраивает. Для преодоления проблемы цех либо депремируют, либо будут использованы другие действенные карательные механизмы. Поскольку менее производительные участки не в состоянии работать быстрее, попытка ускорения их работы приводит к неизбежному росту брака и технологических отходов. Возражения службы качества при этом в расчет не принимаются, поскольку приходится отвечать за более важные, с точки зрения руководства, показатели «закрытия позиций заказа» и НЗП.
Для того чтобы по максимуму увеличить пропускную способность медленных участков, производственный график планируется с минимальным количеством переналадок. В результате на адъюстаже накапливается большое количество неукомплектованных позиций заказов (3).
Металл на адъюстаже постепенно заполняет все доступные временные зоны хранения. Ячейки заполняются в несколько ярусов. Часто для того чтобы скомплектовать необходимую позицию заказа пакетом, который лежит на самом дне ячейки, стропальщикам необходимо переложить до пяти пакетов и потом сложить их обратно в ячейку (4). В таких условиях скорость работы адъюстажа замедляется в несколько раз. В итоге скорость исполнения заказов резко падает, заказы закрываются с большим опозданием и уровень НЗП становится максимальным. Сложившаяся ситуация часто вынуждает стропальщиков и кладовщиков закрывать позиции заказа доступными (не заваленными) пакетами с приблизительно сходными с заявленными характеристиками, что в итоге приводит к пересортице на складе и претензиям клиентов.
Поскольку адъюстаж является в некотором смысле пограничной зоной между цехом и складом готовой продукции, руководство завода, пытаясь решить возникшую проблему, может принять решение об использовании склада готовой продукции под хранение неукомплектованных позиций сданного цехом металла (6). В итоге это приводит к перегрузке склада готовой продукции — он растет в высоту. Нарушаются нормы хранения металла. Стропальщики вынуждены помногу раз перекладывать металл с места на место, для того чтобы погрузить нужный пакет в автомобиль. Из-за высоких штабелей часто происходят несчастные случаи и производственные травмы. Производительность участка погрузки становится еще одной проблемой.
Низкая скорость погрузки автомобилей вызывает большое количество нареканий со стороны клиентов. Вынужденные простои автомобилей и ж/д вагонов делают завод непривлекательным, в первую очередь, для средних и малых клиентов, наиболее остро заинтересованных в своевременности выполнения заказов и сопутствующих затратах.
Исчерпав емкость склада готовой продукции, в цехе возникают стихийные зоны хранения металла. Он хранится в несколько ярусов на полу с нарушением норм (7). Отсутствие структурированных зон хранения приводит к частым потерям металла. Это, в свою очередь, снижает и без того низкую скорость комплектации заказов и увеличивает межоперационные издержки за счет поиска нужного металла и внутренних цеховых перемещений.
В итоге производительность цеха падает, уровень НЗП максимален, заказы подолгу застревают в производстве и клиенты не довольны оперативностью работы склада готовой продукции.
Ирония ситуации состоит в том, что цеха, использующие современные автоматизированные участки, более предрасположены к эффекту несбалансированного производства, чем их собратья, применяющие большое количество ручного труда. У человека всегда существует естественный ограничитель производительности — лень. И резерв производительности в лице энергичного мастера смены. Именно поэтому западные производства стараются не загружать на 100%, нивелируя дисбаланс мощностей общим уровнем загрузки 50—60%.
Инструменты затратоискателя
Процесс управления затратами основывается на понимании глубинных причинно-следственных связей производственного и коммерческого процессов металлургического завода. Именно поэтому нашу компанию часто приглашают для разработки методик управления и калькулирования затрат для различных металлургических заводов.
Однако можно выделить наиболее удачные комбинации инструментов, позволяющих реализовать процесс управления затратами в полном объеме.
Управление затратами, в первую очередь, начинается с постановки систем прослеживания, позволяющих получать оперативную информацию по движению металла по всем производственным переделам. В рамках этой системы решаются такие вопросы, как механизмы маркировки и идентификации металла, оперативный учет трудозатрат и нормирование, управление НСИ.
Как правило, самые большие затраты скрываются в малых объемах. Поэтому задача по превращению цеха из черного ящика в открытый для анализа производственный процесс — первостепенна.
Второй фазой управления затратами является внедрение систем бюджетирования и бюджетного планирования. Причем наибольший эффект возникает именно тогда, когда система прослеживания предоставляет в систему бюджетирования точный факт с необходимой степенью детализации.
Начинающим затратоискателям
В этой статье хотелось бы показать не только способы снижения затрат на металлургическом заводе, но и наглядно продемонстрировать увлекательность и важность самого этого процесса.
Главные затраты сегодня кроются не в станках, а в головах. Но, с другой стороны, это означает, что зарабатывать деньги можно, просто научившись мыслить по-другому. Если финансист задумается о том, как на самом деле производится металл, не стараясь рассматривать цех как черный ящик; если производственник задумается о том, сколько стоит то, что он создает, или попробует думать, как коммерсант, тогда и начнется процесс управления затратами.
Удачи вам, затратоискатели!
ООО «БДО Юникон Консалтинг» — ведущая национальная консалтинговая компания, оказывает услуги в области управленческого, ИТ-консалтинга и внедрения технологий управления на базе решений ведущих мировых производителей ERP-систем. Входит в группу компаний БДО Юникон (создана в 1989 г.). По результатам рейтингов занимает одно из лидирующих мест в десятке крупнейших консалтинговых компаний России.
В активе БДО Юникон Консалтинг — свыше 1 тыс. проектов управленческого и ИТ-консалтинга, из них более 150 — по созданию интегрированных систем управления на базе SAP, Oracle, Microsoft Dynamics AX. БДО Юникон Консалтинг признана лучшим партнером SAP по итогам 2006 г. и имеет несколько статусов партнерства с компанией SAP: mySAP Local Alliance Partner, SAP Service Alliance Partner, SAP Content Preferred Partner в области налогового учета (первой в России) и SAP Industry Preferred Partner для предприятий нефтяной и газовой промышленности. Также является сертифицированным партнером Oracle и Microsoft.
Услуги БДО Юникон Консалтинг сертифицированы на соответствие международному стандарту качества ISO 9001.
Дополнительную информацию можно найти на официальном сайте компании БДО Юникон Консалтинг по адресу: www.bdo.ru, www.unicon-ms.ru.
Дополнительные
материалы:
|
|